Clean Room Requirements for Computer Hardware
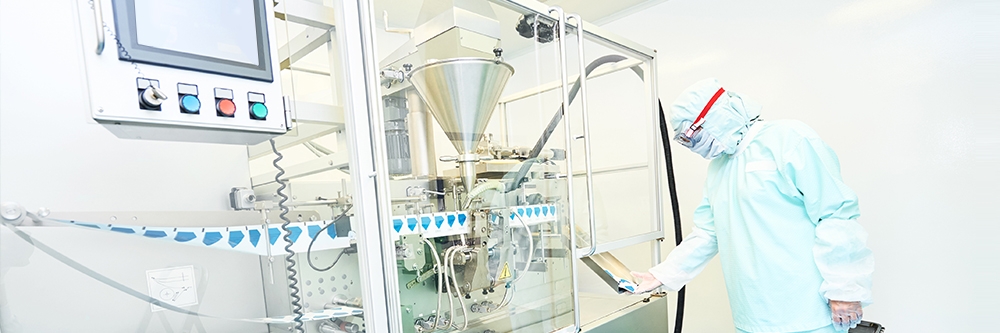
What is a Clean Room?
A clean room is an environment where airborne contaminants (dust, microbes, and particles) are highly controlled. The number of particles in the air and the size of particles in the air are kept below specific thresholds, and those thresholds depend on the class of the clean room.
Applications for Clean Rooms
Clean rooms are used for applications such as food manufacturing, pharmaceutical production, aerospace engineering, and biomedical research, because even a microscopic contaminant can adversely affect these processes.
Classes of Clean Rooms
Classes of clean rooms are set by the International Organization for Standardization (ISO). ISO sets standards for many industries, including food and drug manufacturing, and computer hardware manufacturing (Teguar is ISO 9001:2015 certified).
The ISO clean room classes set the threshold for the number of particles in the air, per cubic meter (particles/m3). The limits are different for different sized particles. The particles range from 0.1 μm to 5 μm in diameter (μm is a micrometer, also called a micron. It is equal to 0.001 mm, or about 0.000039 inch. As defined by Britannica).
To put that number in perspective, the human eye cannot see anything smaller than about 40 μm. Human hair is about 50-100 μm in diameter and bacteria are about 2 μm in diameter. See the table below from Hastings Filters, to see some other comparisons.
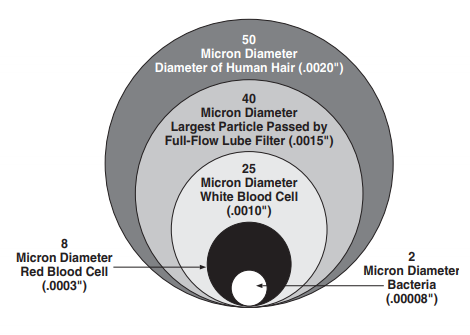
The classes range from class 1, being the cleanest and most highly filtered, to class 9, which is the typical ambient air around us every day. The table below by Cleaning Maintenance Management displays the concentration limits per particle size, for each class.
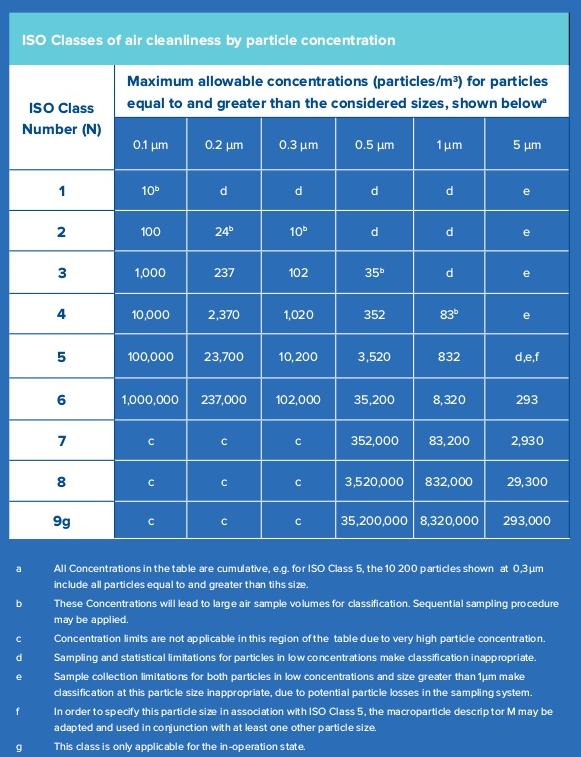
Up until 2001, standards for clean room environments were set by the Federal Standard 209E (FED-STD-209). You may still see some clean room manufacturers use the term “class 10,000 clean room” to refer to an ISO Class 7 clean room. FED-STD-209 was officially replaced by ISO standards in 2001. The table below shows the FED-STD-209 equivalent to the new ISO classifications.
ISO 14644-1 | FED-STD-209E |
Class 1 | N/A |
Class 2 | N/A |
Class 3 | Class 1 |
Class 4 | Class 10 |
Class 5 | Class 100 |
Class 6 | Class 1,000 |
Class 7 | Class 10,000 |
Class 8 | Class 100,000 |
Class 9 | N/A |
How to Maintain a Clean Room Environment?
Clean rooms are maintained by highly specialized ventilation systems. Unlike ventilation in a normal environment, in a clean room, the air flow is unidirectional. This means there cannot be any fans (such as those inside a typical computer), which push air around, as this will interfere with the unidirectional movement of the clean room ventilation system. Clean rooms use either High-Efficiency Particulate Air (HEPA) or Ultra-Low Particulate Air (ULPA) filters in their ventilation system.
The clothing that clean room personnel wear is also highly regulated. According to Clean Air Technology, Inc., required “cleanroom garments [can] include boots, shoes, aprons, beard covers, bouffant caps, coveralls, face masks, frocks/lab coats, gowns, glove and finger cots, hairnets, hoods, sleeves and shoe covers.
Depending on the class of the clean room, personnel may be required to enter an “air shower” before entering the cleanroom. This is a separate room that blows dust and particles off of the person, before he or she enters the clean room environment. Personnel cannot wear makeup or perfumes and are required to cover their hair. This article from Production Automation Corporation describes a typical process that clean room personnel undergo before entering a clean room; it’s a 43 step process.
Computer Hardware Requirements for Clean Room Manufacturing
For food and beverage manufacturing and some pharmaceutical production environments, computers must be able to withstand daily wash-downs. Equipment is sanitized with high-pressure, high-temperature water jets. Computers in these environments are made with grade SUS304 stainless steel, which is rust-proof and anti-corrosion. Some environments require a higher grade SUS316L stainless steel, which will not corrode, even to salt water. These computers are fully sealed and rated IP69K waterproof, so they will not allow any liquid to enter the computer, even with water jets spraying from all angles.
In applications such as biomedical research and aerospace engineering, equipment is not usually sprayed with water jets, but is wiped down frequently with disinfectants. In this case, the computer needs to be able to withstand strong chemical disinfectants, which consumer-grade computers cannot. Computers in these applications can be built with stainless steel or medical-grade plastic. Medical-grade plastic will not corrode or degrade from the frequent use of disinfectants, and it is built with antimicrobial properties. Learn more antimicrobial and medical-grade computer housings in this Teguar article.
Whether the computer is made with antimicrobial plastic or stainless steel, it must have a fanless cooling system. Clean room computers should also be designed with minimal crevices, where dust and particles build up. Full-flat front bezels minimize crevices and edges and are easier to spray and clean.
Many clean room manufacturers choose Teguar’s all-in-one, waterproof touchscreen computers, because they can be customized to their application and can integrate peripherals like speakers and barcode scanners. This is beneficial for clean rooms, because peripherals take up space and add time to the cleaning process. The touchscreen also eliminates the need for an external keyboard and mouse.
To learn more about cleanroom computers, view Teguar’s Clean Room Application Page, our Stainless Steel Computers, Medical Computers, or contact us to discuss your project.