From Smart Factories to Industry 4.0: The Evolution of Industrial Computers in Manufacturing
TL/DR
- Industrial computers have played a critical role in the evolution of manufacturing, from early process control and automation to the current Industry 4.0 movement.
- Industrial computers enable manufacturers to automate, optimize, and improve production processes, and the latest technologies such as the IIoT, robotics, data analytics, and predictive maintenance have transformed the manufacturing landscape.
- These advancements have resulted in more efficient, flexible, and customer-centric production systems, which are critical to meeting the demands of modern manufacturing.
- Industrial computer solutions provider Teguar offers products designed to provide real-time monitoring and control of critical manufacturing processes, helping manufacturers improve efficiency, reduce downtime, and increase overall productivity.
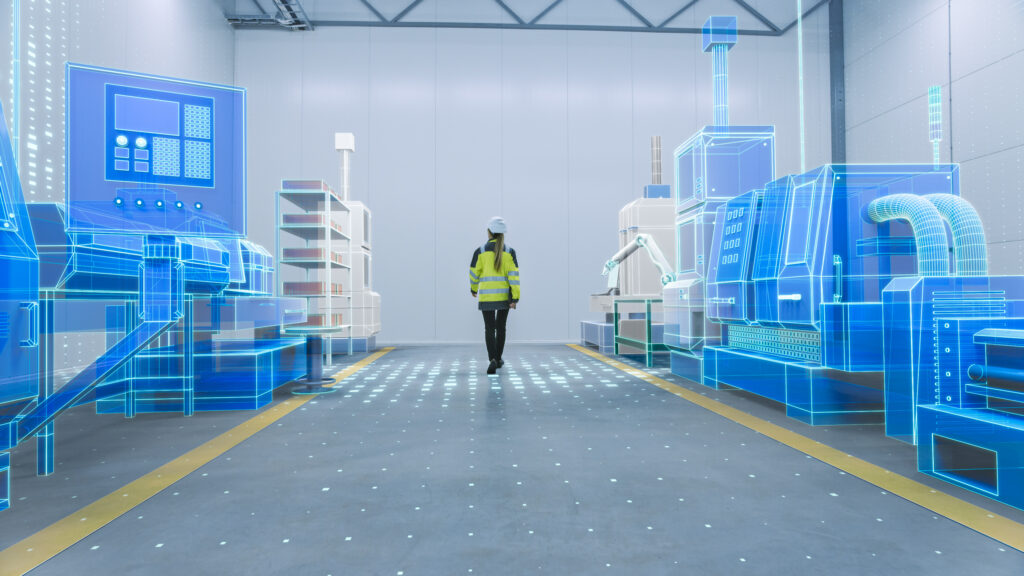
Industrial computers have become an essential component of modern manufacturing, providing the technology needed to automate, optimize, and improve production processes. From early process control and automation in the 1960s and 70s to the current Industry 4.0 movement, the evolution of industrial computers has been remarkable. In this article, we explore the development of industrial computers and their role in modern manufacturing.
Early Industrial Computers: Process Control and Automation
In the early days of manufacturing, industrial computers were primarily used for process control and automation. These computers were expensive and bulky, requiring significant space and maintenance. However, they provided manufacturers with a level of control that was previously impossible, allowing them to automate and optimize processes in ways that were previously unimaginable.
Embedded Systems: Specialized Computing for Industrial Applications
As technology advanced, industrial computers became smaller and more cost-effective, making them accessible to a wider range of manufacturers. This led to the development of embedded systems, which are specialized computers designed to perform a specific task or set of tasks. These systems are often used in industrial settings, where they provide real-time monitoring and control of critical processes.
The Industrial Internet of Things (IIoT): Networked Devices and Real-time Data
The Industrial Internet of Things (IIoT) is a network of connected devices, sensors, and machines that communicate with each other to optimize production processes. These devices are equipped with sensors that collect data, which is then analyzed and used to make real-time decisions about production. The IIoT has enabled the development of predictive maintenance systems, which use data analytics to predict when equipment is likely to fail. By identifying potential issues before they occur, manufacturers can schedule maintenance and repairs, minimizing downtime and increasing overall efficiency.
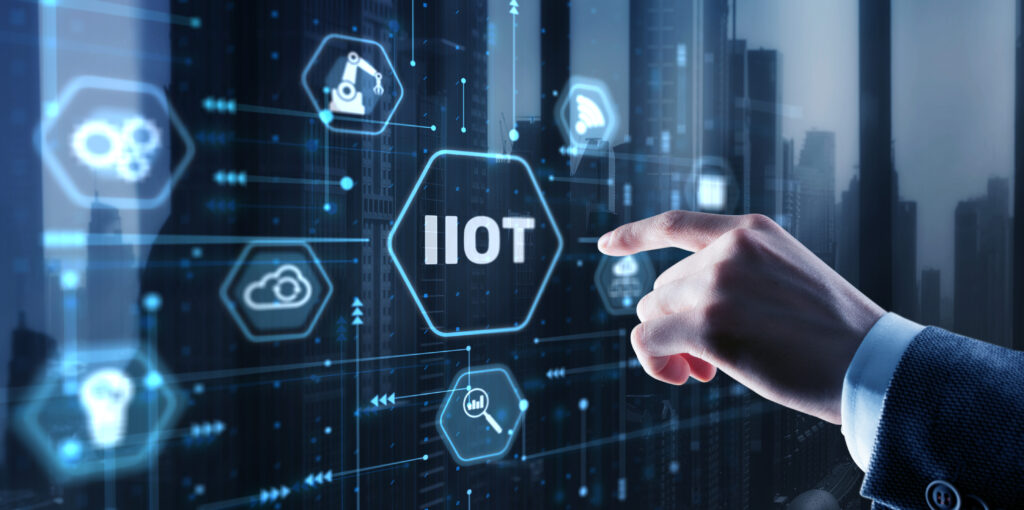
Human Machine Interface (HMI): Graphical Interface for Real-time Process Control
Human Machine Interface (HMI) systems provide a graphical interface for operators to interact with production equipment and monitor processes in real-time. HMIs have revolutionized the way we approach process control, making it easier for operators to identify potential issues and make real-time adjustments.
Industrial Communication: Enabling Information Sharing
Industrial communication refers to the systems and protocols used to enable information sharing between devices and systems in a manufacturing environment. These systems include Ethernet, Profibus, and other specialized protocols that enable real-time data exchange between machines and other systems.
Robotics: Automated Systems for Manufacturing
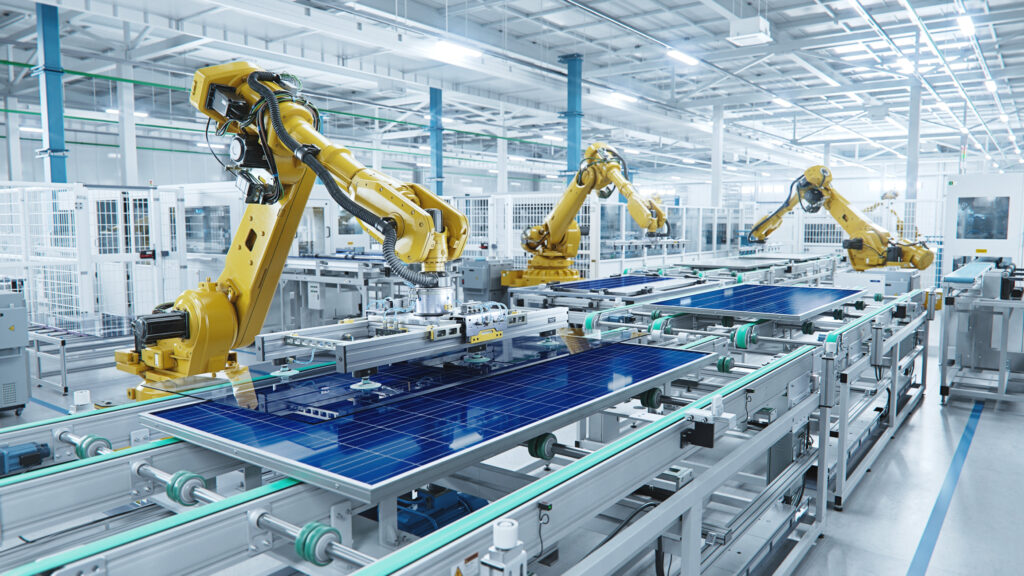
Robotics has become an increasingly important component of modern manufacturing. Industrial robots are used for everything from assembly to packaging, reducing the need for manual labor and improving efficiency. These robots are often integrated with other systems, such as HMIs and predictive maintenance systems, to create a fully automated production line.
Data Analytics and Predictive Maintenance: Improving Efficiency
Data analytics has become a critical tool for manufacturers, enabling them to gather insights from real-time data to optimize production processes. Predictive maintenance systems use machine learning algorithms to analyze data and predict when equipment is likely to fail. By identifying potential issues before they occur, manufacturers can schedule maintenance and repairs, minimizing downtime and increasing overall efficiency.
Quality Control: Ensuring Consistent Production
Quality control is an essential component of manufacturing, ensuring that products are produced to a high standard of quality. Industrial computers play a critical role in quality control, providing real-time monitoring and control of production processes. This allows manufacturers to identify potential issues early on and make adjustments to ensure consistent quality.
Supply Chain Management: Connecting Production to the Marketplace
Industrial computers also play a critical role in supply chain management, providing real-time data and insights into production processes. This enables manufacturers to optimize production based on demand, ensuring that they can meet customer needs while minimizing waste.
Industry 4.0: The Future of Manufacturing
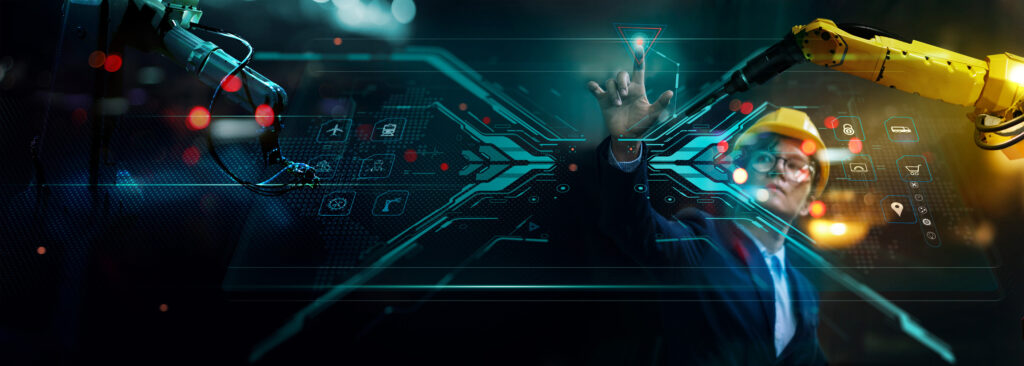
Industry 4.0 is the latest evolution of manufacturing, integrating advanced technologies such as the IIoT, robotics, and data analytics to create a fully connected, intelligent production system. Industry 4.0 is all about creating a more efficient, flexible, and customer-centric manufacturing process, enabling manufacturers to respond quickly to changing demand and market conditions.
Conclusion: The Evolution of Industrial Computers in Manufacturing
From early process control and automation to the current Industry 4.0 movement, the evolution of industrial computers has been remarkable. Industrial computers have become an essential component of modern manufacturing, providing the technology needed to automate, optimize, and improve production processes. As we look to the future, it’s clear that industrial computers will continue to play a critical role in the evolution of manufacturing, enabling manufacturers to create more efficient, flexible, and customer-centric production systems.
Teguar‘s products are ideal for manufacturers looking to improve efficiency, reduce downtime, and increase overall productivity. By leveraging the latest technologies such as the IIoT, data analytics, and predictive maintenance, Teguar’s products enable manufacturers to create more intelligent, connected production systems. As such, Teguar’s products are highly relevant to the evolution of industrial computers in manufacturing, and serve as an excellent example of how technology can be leveraged to create more efficient and effective manufacturing processes.
Teguar is a leading provider of industrial computer solutions, offering a wide range of products that can be used in a variety of manufacturing settings. Teguar’s products include rugged tablet PCs, industrial panel PCs, and embedded systems, all designed to provide real-time monitoring and control of critical manufacturing processes.