7 Most Common Reasons for Industrial Computer Failure and How to Avoid Them
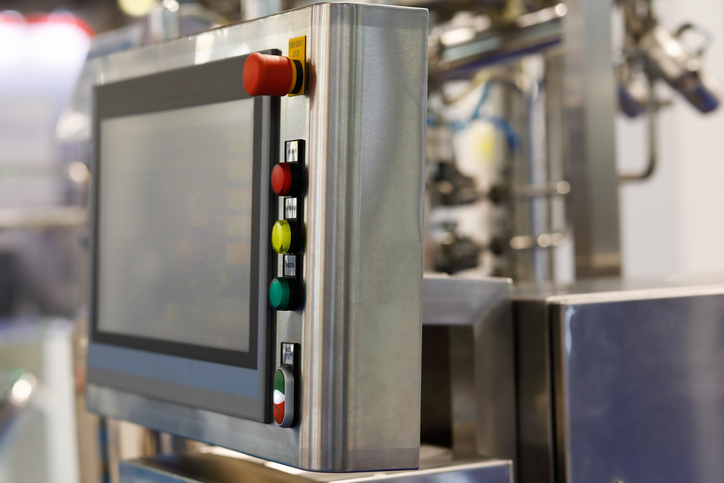
At the heart of modern industries, industrial computers serve as the backbone, directing crucial processes and ensuring seamless operations. These robust machines, however, are not impervious to failure, and when they do falter, the consequences can be dire—costly downtime, productivity losses, and compromised safety. Understanding the most common reasons for industrial computer failure is crucial for businesses to proactively mitigate risks and maintain optimal performance. In this article, we will dive into the primary causes of computer failure in industrial settings and provide practical tips to avoid them. We will also explore effective measures to repair and safeguard operations in the event of a computer breakdown.
1. Overheating and Poor Ventilation
Industrial computers, operating in demanding environments, are susceptible to overheating, which can lead to malfunctions and failures. Overheating occurs when the internal components of a computer reach temperatures beyond their designed limits. This can be exacerbated by poor ventilation, a common issue in industrial settings with high ambient temperatures and inadequate cooling systems.
To prevent overheating, regular cleaning and maintenance of cooling systems are paramount. Dust and debris accumulation on cooling components can impede airflow, causing temperatures to rise. Proper placement and positioning of industrial computers, ensuring sufficient space for airflow, also contribute to preventing overheating. Employing external cooling mechanisms, such as fans or liquid cooling systems, can provide an additional layer of protection against heat-related failures.
2. Dust, Dirt, and Contaminants
Dust, dirt, and contaminants pose a significant threat to industrial computers, infiltrating sensitive components and causing malfunctions. In industrial settings, where particulate matter is abundant, these contaminants can accumulate on circuit boards, connectors, and other crucial parts, leading to short circuits and component failures.
Mitigating the risks of dust and dirt involves implementing regular cleaning and maintenance routines. Cleaning industrial computers using compressed air or specialized cleaning tools helps remove accumulated debris. Implementing air filtration systems in computer rooms can significantly reduce the influx of contaminants. For added protection, enclosing computers in dust-resistant cabinets creates a physical barrier against external pollutants.
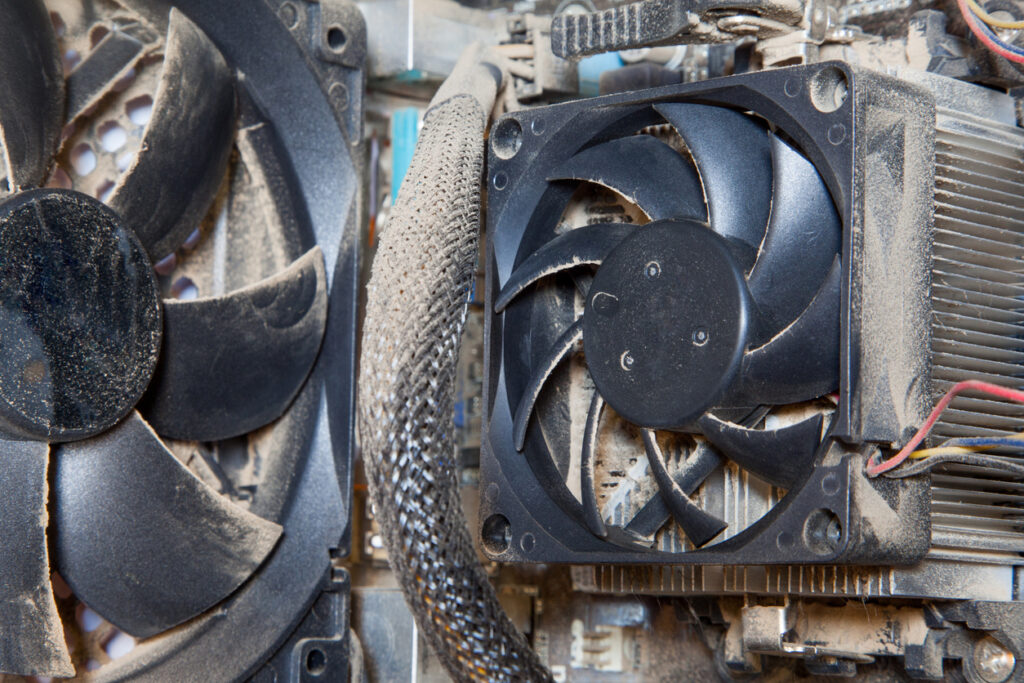
3. Power Surges and Electrical Issues
Power surges and electrical issues are notorious culprits for damaging industrial computers. Fluctuations in voltage, sudden power outages, or electrical interference can compromise the integrity of computer components, leading to failures and data corruption.
Protective measures to prevent electrical damage include the installation of surge protectors and voltage regulators. These devices act as a buffer against sudden spikes in voltage, diverting excess energy away from the computer. Regular inspections of electrical systems, identifying and addressing potential issues, contribute to a stable power supply. Implementing backup power supply systems, such as uninterruptible power supply (UPS) units, ensures continuous operation during power fluctuations or outages.
4. Inadequate Maintenance and Insufficient Upgrades
Regular maintenance and timely upgrades are indispensable for the longevity and reliability of industrial computers. Neglecting these essential tasks can result in gradual deterioration, leading to unforeseen failures and disruptions.
Developing a comprehensive maintenance schedule and checklist is a best practice to ensure all components are inspected and serviced regularly. Keeping software and firmware up to date with the latest releases and patches is crucial for addressing security vulnerabilities and improving system stability. Regular hardware inspections and replacements, especially for aging components, prevent potential points of failure and extend the lifespan of industrial computers.
5. Environmental Factors: Temperature and Humidity
Extreme temperature and humidity levels can adversely affect the performance and lifespan of industrial computers. Operating outside the recommended temperature and humidity ranges specified by manufacturers can lead to overheating, condensation, and corrosion.
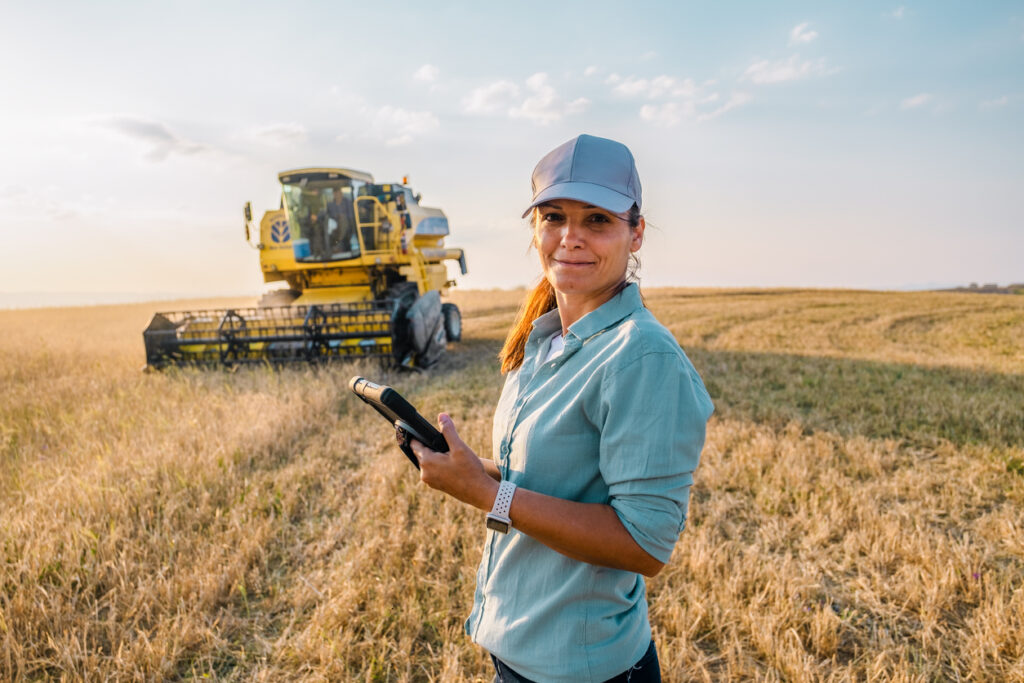
Maintaining appropriate temperature and humidity levels involves implementing climate control systems in computer rooms. These systems regulate the environmental conditions to ensure optimal operating conditions for industrial computers. Monitoring and alert systems that notify operators of temperature and humidity changes allow for swift corrective actions. Isolating computers from extreme environmental conditions, such as placing them in sealed enclosures with controlled climates, provides an additional layer of protection.
6. Software and Compatibility Issues
Software-related problems are common contributors to industrial computer failures. Incompatibility between software and hardware components can result in system crashes, data corruption, and overall instability.
To address software and compatibility challenges, thorough research on software compatibility should be conducted before installation. Regularly updating software and drivers ensures that the latest features and bug fixes are applied, reducing the risk of compatibility issues. Testing new software in a controlled environment before full deployment allows for the identification of potential conflicts and ensures a smoother integration into the industrial computing environment.
7. Industrial Computer Repair
Despite the best preventive measures, industrial computers may still encounter failures. Timely and effective repair is crucial to minimizing downtime and restoring operations swiftly. Recognizing the signs indicating the need for professional repair services, such as unusual noises, error messages, or hardware malfunctions, is key to proactive intervention.
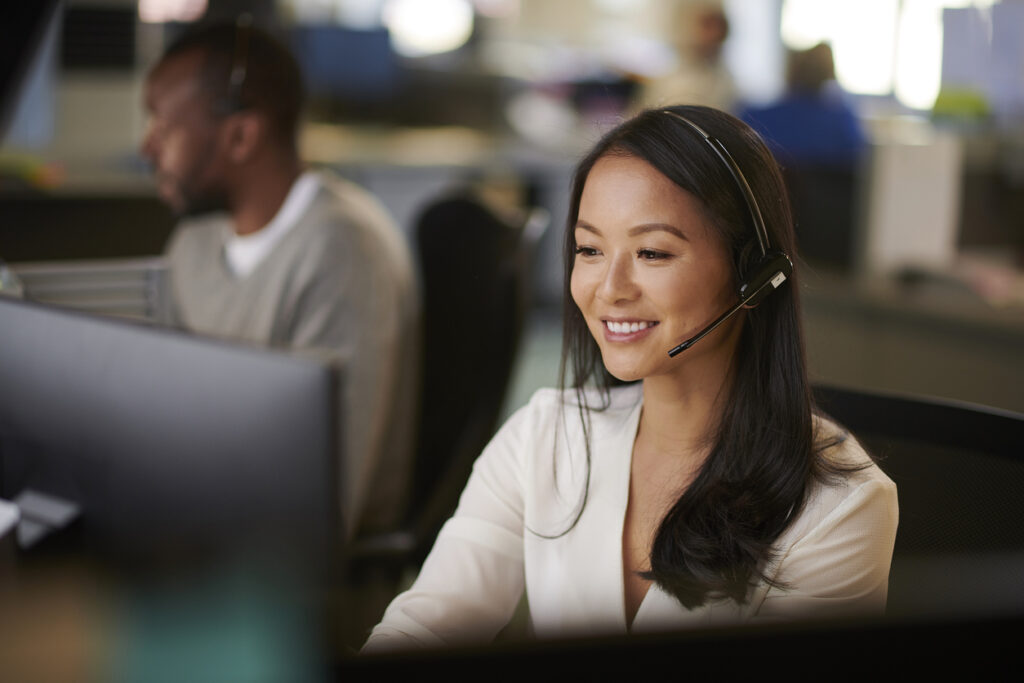
When facing computer failure, diagnostic procedures should be employed to identify the root cause of the issue. Engaging qualified industrial computer repair specialists ensures that the correct solutions are applied, and repairs are conducted with precision. Implementing preventive measures post-repair, such as reinforcing protective measures and updating maintenance schedules, helps fortify the system against future failures.
Navigating Failures
In the intricate dance of industrial operations, industrial computers are the choreographers, orchestrating processes seamlessly. However, their reliability is not guaranteed, and understanding the most common reasons for their failure is paramount for businesses seeking uninterrupted operations. From overheating and dust infiltration to power surges and software conflicts, each potential hazard can be mitigated through proactive measures.
This article has explored these hazards in depth, offering practical tips to avoid industrial computer failure and maintain optimal performance. By adhering to preventive strategies, such as regular maintenance, environmental controls, and software updates, businesses can significantly reduce the risk of disruptions. In the event of a failure, timely and effective repair, coupled with post-repair preventive measures, ensures a swift return to operations.
The path to industrial computer reliability is paved with proactive measures and a keen understanding of potential risks. By implementing the tips and suggestions provided, businesses can navigate this path with confidence, ensuring the uninterrupted performance of their industrial computers in dynamic and challenging environments.