Teguar Partners with LivaNova to Design Computer Hardware for Next-Gen Perfusion System
When global medical giant LivaNova reached out to Teguar in search of a suitable patient monitor for their Essenz Perfusion System, Teguar knew it was possible to build exactly what they needed.
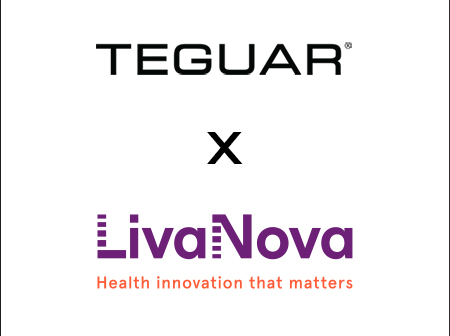
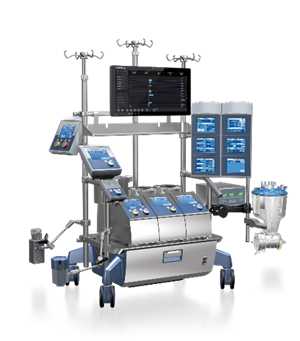
LivaNova is a global medical technology company that ‘specializes in products and therapies for the head and heart’, as they explain in their company profile on their website. Their medical equipment can be found in healthcare facilities across more than 100 countries worldwide, and their employee count is approximately 1,000.
The end users of LivaNova’s medical systems are healthcare professionals who provide a diverse range of care in multiple fields. Devices manufactured by LivaNova are designed to treat a myriad of complex health issues, such as heart failure, drug-resistant epilepsy, obstructive sleep apnea, difficult-to-treat depression, and more. But the specific reason that LivaNova reached out to Teguar was in their search of a patient monitor for their new state-of-the-art perfusion system.
This machine takes over the processes of respiration and blood circulation for a patient while they’re undergoing surgery. In other words, the stakes have never been higher.

The Challenge
LivaNova was seeking the computer hardware component needed for their new perfusion system, which was in development at the time. This monitor would be used by clinicians using the system during cardio-pulmonary bypass procedures.
Getting Started
When initiating a project like this, it is essential to have a thorough understanding of exactly what the customer needs. Clint Nichols, Business Development Manager for this project, talks about what it was like to tackle a job as important as this one.
“When starting a project as big as the LivaNova Essenz Patient Monitor, we start by looking at the total scope of the project. Teguar’s products and services are based around three different scenarios: off-the-shelf units, modifying present products per customers’ requirements, and complete ground-up development. For the LivaNova project, we had an off-the-shelf unit that met the majority of their requirements. This gave us a good base product to start the design.
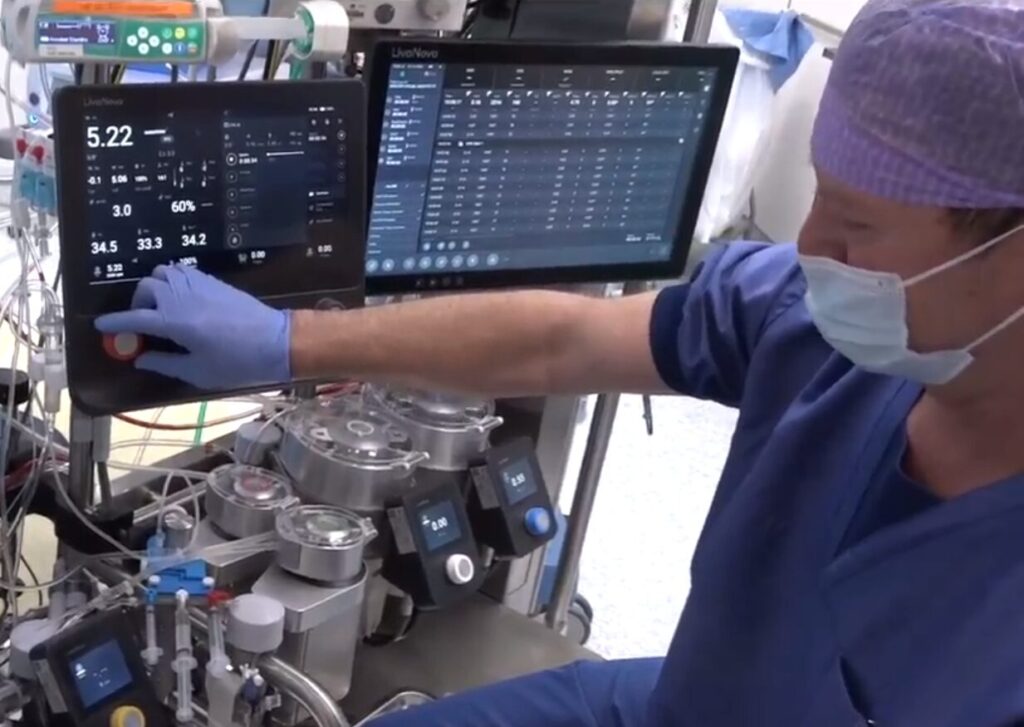
Essenz Patient Monitor being used in surgery for the first time
“Medical products in general need to be supported long term (5-7 years). Selecting the right components from the right suppliers is of most importance. Having a team with 25 years of experience is a huge benefit. It’s important to understand the customer’s complete expectations, timelines required, as well making everyone aware of the resources needed to bring a product like this to market.”
-Clint Nichols, Teguar’s Healthcare Business Development Manager & LivaNova Project Lead
Project Requirements
In simple terms, LivaNova needed a fleet of medical computer hardware with customizations. With plans to mass produce their patented perfusion system and sell hundreds of systems to healthcare providers around the world, logistical factors like product availability (both short and long term), inventory levels and lead times were essential parts of making the project work.
Though Teguar’s medical computers are powerful tools straight out of the box, LivaNova had a number of specific requests for their monitor component, including (but not limited to):
- Upgraded touchscreen
- Custom logo on front bezel (white label services)
- Custom logo on boot screen
- Customized function keys
- Isolated I/O ports
- Removable batteries capable of maintaining at least 6 hours of backup battery life
- Custom color housing
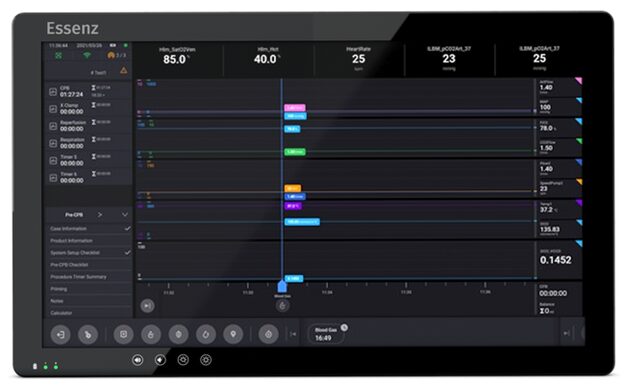
In addition to these customizations, certain expectations reasonable for any medical computer were also required, including an IP rating sufficient for regular washdowns, adherence to stringent reliability tests, and medical certification requirements.
Starting with an Off-the-Shelf Solution…
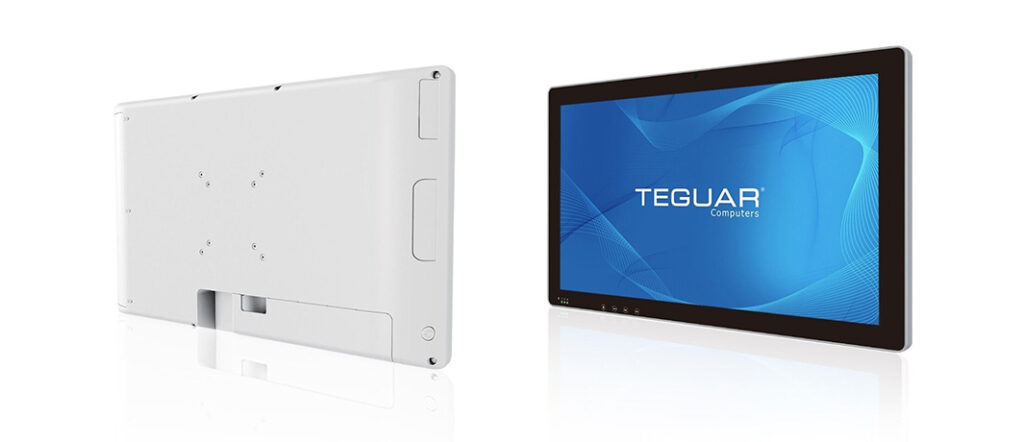
To begin, Teguar proposed using the TME-5040-22 as a starting point for the customizations, which was a great fit for several reasons. As a Teguar-brand medical computer, this device met all medical certifications required for the project, and the 21.5″ Full HD widescreen provided plenty of visual real estate to display patient vitals.
Additionally, in true Teguar fashion, it was important that the unit have a clean, sleek look. As part of a larger system meant for resale, it needed to be aesthetically pleasing, not like your average clunky medical computer or cheap consumer-grade PC. The TME-5040-22 satisfied this requirement nicely.
Using this unit as a base, Teguar’s product managers were now ready to make modifications based on LivaNova’s specific requests.
…And Adding Customizations
On this project, the product design specialist team worked meticulously alongside LivaNova experts to ensure that all their requirements were satisfactorily met. This required extreme time dedication across both teams, all for the mission to support perfusionists and their patients during life-saving procedures.
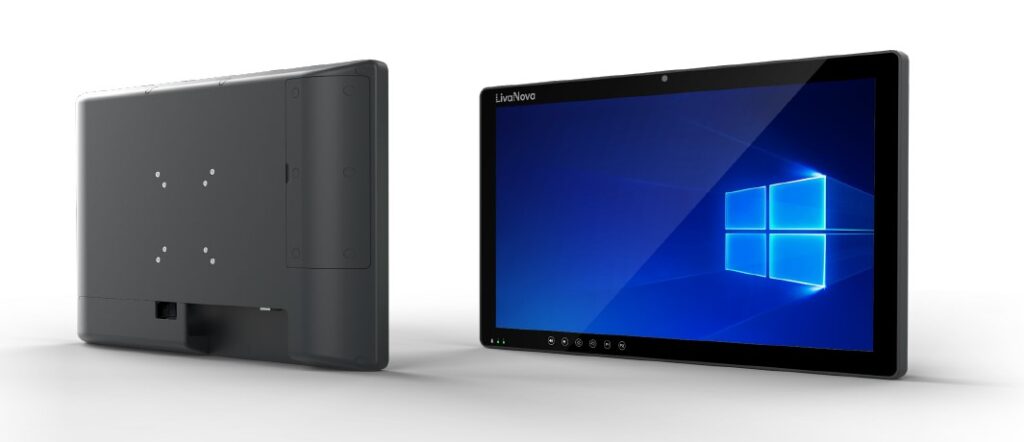
The final results: the innovate monitoring system embedded in the Essenz Perfusion System.
The Essenz Patient Monitor is a medical device that provides continuous, advanced, and insightful data through one centralized screen that can be configured to show the key parameters at all times during a case. Continuous is the key here since this device is used during life-saving open heart surgical procedures, and oxygen needs to be continuously pumped through the body. This means the hardware used in this device cannot be just a consumer grade PC; it must be able to withstand vigorous hours of usage.
Contributing to the development of the Essenz Patient Monitor is just a glimpse into the custom projects Teguar is capable of. Mechanical engineering, electrical engineering, software development, and certification are all part of Teguar’s custom projects portfolio. If you have a custom project, please contact our product specialists by calling (866) 738-4698 or contacting us online.
For important safety information visit essenzperfusion.com.
Teguar’s Medical OEM Services
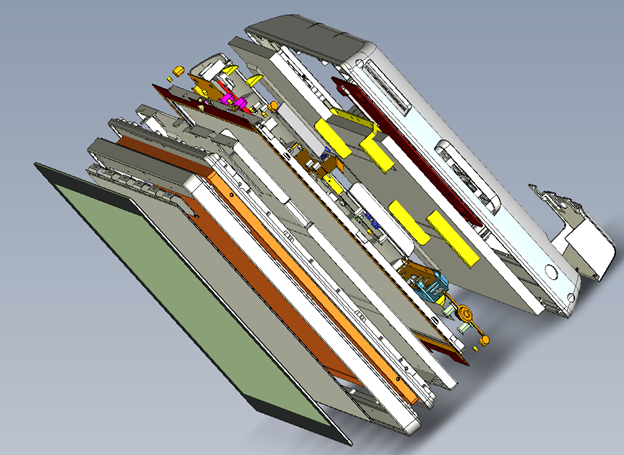
When working with Teguar on a custom project, you are working alongside a strong and knowledgeable engineering team to help bring your product to life. Custom project timelines, product resources, and prototypes with strict protocol tests are all processes used in the custom project pipeline at Teguar.
As a powerhouse in the medical and industrial computer industry, Teguar has accrued quite a few experiences with custom jobs. Whether it is as small as adding additional inputs and outputs, or as large as a complete redesign with custom certification, the team can make it happen.
The healthcare space often needs equipment available for years to come. In a partnership with Teguar, custom computer components are available for the long-term. Our global locations in Taiwan, Switzerland, and the USA helps meet our customer needs worldwide.